Robots have now spread like wildfire in many industrial production sectors all over the world, from the food to the cosmetic sector and even in the agri-food sector. In fact, many farms decided to use 4.0 agriculture technologies to improve the quality of work.
In 2018, 2.8 billion dollars were invested in innovative companies in agritech and around 170 million were used for the development of drones and robots in agriculture, as well as self-driving tractors capable of automating some operations carried out by humans.
Some practical examples are the robot for the pruning of the fruit trees or vines and intelligent systems able to recognise a diseased plant and direct the jet of medicinal products directly on it. Let’s see more in practice how robots will transform agriculture 4.0.
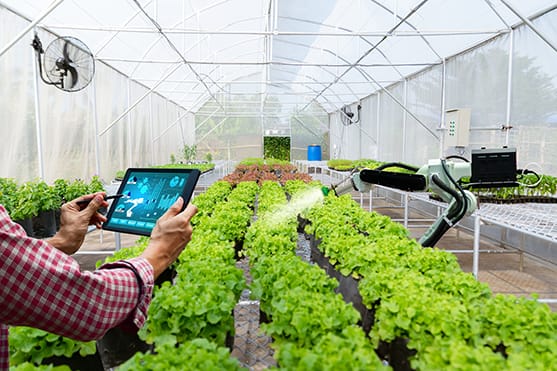
BENETIFS OF USING ROBOTS FOR AGRICULTURE
Let’s start with 4 reasons why robots are useful:
- They collect a non-standardised product, so the farmer is not forced to employ new manpower every year during the harvest;
- They prevent potentially dangerous operations for workers, such as administering of phytosanitary products for antifungal treatments;
- Thanks to the parallel guide, the worker does not need to correct the trajectory of the vehicle;
- By the use of cameras and image recognition algorithms, the agritech equipment identifies weeds, insects or diseased plants, taking also precise measurements.
All this means less consumption of products, which lead to lower costs for the farmer and a high level of sustainability.
Agrifood tech and nutrition
To date, tractors work using diesel and the equipment connected to them are driven by the power take-off and the hydraulic system. The tractors of the future will use green sources of energy, such as electricity.
For self-driving tractors, biogas generated independently by the farmer thanks to the exploitation of biomass could be a good solution. Thus, each farm will have a small biogas plant, in addition to simple plants.
Robots engaged in operations such as precision weeding or pruning, will used electric power because it is less expensive and it needs less maintenance. Think of the wheels that advance the vehicle on the field, the sensors, the clamp for precision picking and the solar panels above the robots.
Connectivity of agritech systems and economic sustainability
Intelligent robots are not allowed to move on the field without supervision both for safety reasons and for agronomic reasons. A robot could hit something or someone and create serious damage, or a malfunction can destroy a year of work.
For this reason, the farmer will most likely supervise the machines from different monitors in the future, as long as there is a 5G connection in the countryside, which speeds up the time between sending a command and receiving it. Thus, the farmer just touching the joystick will be able to adjust the trajectory of the tractor, support an automatic pruner or harvester in the case of a complication.
The high cost remains one of the main limits of these machines, sensors and robots. The prototypes made so far are still slow, expensive and unable to adapt to unpredictable environmental conditions. Through artificial intelligence, farm robots can learn to solve problems that have no solution so far.
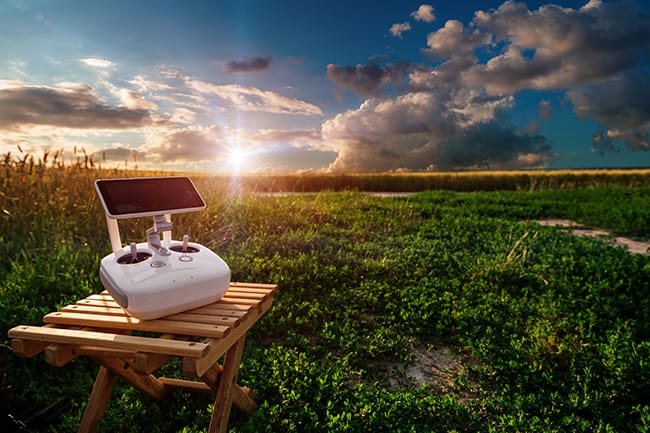
ROBOTIC AGRICULTURE MODELS
Self-driving tractors are one of the sectors in which automation technology is developing more, thanks to the application of GPS and RTK networks. The vehicles in question do not require drivers, they are tractors without cab that move between the vineyards or orchards independently.
As you can imagine, the construction of these vehicles (already used by the Californian startup Bear Flag Robotics or Agribot) is quite expensive, but actually, this is not the only obstacle to solve.
Robotics systems
Robotics systems in agriculture are not simple and intuitive in the user interface. It may be useful to simplify human-machine interaction to facilitate their diffusion. Although everything can still be improved, the work continues to achieve more effective and rapid agriculture, since the current workforce is aging and is increasingly difficult to replace.
Drones also use GPS technology, for example for monitoring vineyards or to eliminate pests from plants. A mini robot can even weed the fields on its own, working up to 12 hours and using only solar energy. It is possible through a system to treat weeds, reducing the use of herbicides that damage crops and avoiding the introduction of chemicals into the environment.
A robot to harvest fruit
Technologies such as agrobots and drones will soon change the fate of agriculture, but they are not the only ones. You can also exploit the potential of collaborative robots, already used in multiple sectors, such as in the strawberry harvest.
In some areas of Great Britain, in fact, more than 20% of the fruits are not harvested due to the lack of manpower and the collaborative robots would partially solve this problem.
Some engineers are studying to enable robots to collect, control and pack fruit in the field, working alongside human personnel but reducing labour costs.
The problems of robots
The difficulties arise from the fact that each fruit has different shape, size and ripening time. Moreover, the environment constantly changes due to atmospheric phenomena, so an efficient manipulation within a non-conventional environment represents a great challenge for robotics.
The robots would carry out operations that are simple for humans to carry out, but since they are artificial systems that always repeat the same actions, they need specific sensors for vision, touch and strength, which correspond to the same human skills as the workers.
Double hands robots, for example, recreate the way humans harvest fruit, with a vision system to identify the fruits hidden behind the leaves and also able to adapt to changes in environmental conditions.
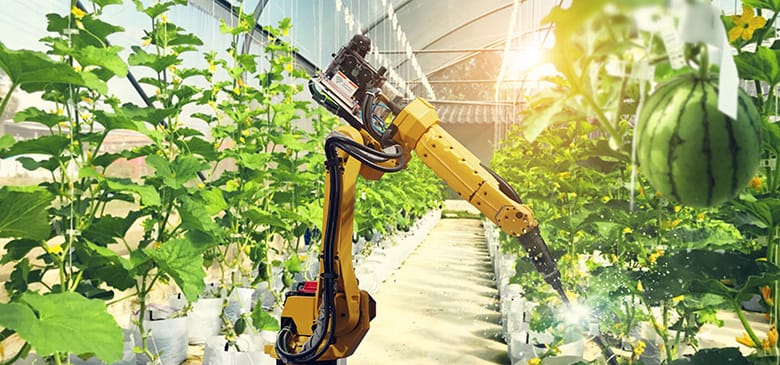
Agriculture made by robots
In 2015 RoDyMan was presented in Naples, the robot that represented the turning point in the work of man and which had the purpose of contributing to progress in the medical field. It was actually a pizza maker robot, designed to develop tactile sensitivity in machines.
Advances in agrifood tech and artificial intelligence lead also to the spread of bartender robots and those capable of growing and producing fruit and vegetables, replacing humans. Certainly, robots for agriculture are an incredible step forward, because they are able to optimise numerous processes, including harvesting.
MEN AND MACHINES, THE ADVANTAGES
The Californian startup Iron Ox has recently started selling the first three vegetables resulting from the work of the machines at the Bianchini’s Market in San Carlos, which specialises in local and organic products.
To automate agricultural work, robotic arms are used for harvesting, hydroponic tanks and robots that take care of the cultivation phase. In the context of this autonomous agriculture, humans are still indispensable, since they package the plants and handle the sowing.
The agrobots used for local agriculture are small in size but they are able to reduce costs and emissions during transport. In a nutshell, these are really km 0 products.
Another advantage is represented by the reduction of risks in the field, given that artificial intelligence allows the detection of parasitic attacks and diseases before their spread. Obviously, also the optimisation of the soil draws its advantages, being able to produce in less space what is normally produced in many more hectares of land.
The future of agriculture made by robots is still uncertain, but for experts in the sector it will develop while remaining a niche reality.
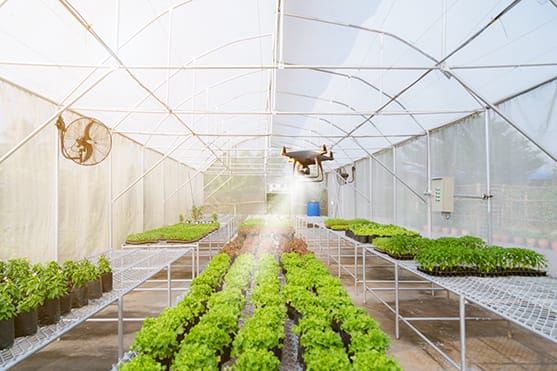
THE IMPORTANCE OF AGRICULTURAL ROBOTICS
In Europe it is becoming difficult to find agricultural workers, because fewer and fewer people are willing to do this kind of job, especially among the young generations. People concentrate in the cities and abandon the countryside also because agricultural work is seasonal and does not ensure the economic stability that many people needs. But at the same time, consumers demand to have all the goodness offered by the earth on their table. For these reasons, agricultural robotics is the right solution, supporting man in sowing and harvesting.
Sowing with agricultural robotics
Researchers from the Israeli University are studying the possibility of using robots in sowing and harvesting. They are developing drones capable of pollinating flowers instead of bees, since their reduction in recent decades requires alternatives that guarantee honey production.
In addition to pollination, smart pesticide sprayers are being developed and they will be able to can calculate the amount of substance useful for preventing plant diseases. It would seem that just a small quantity of product for each plot of land is enough to solve the problem. Engineering are creating a robot capable of sprinkling pesticide only to the affected area, thanks to the preventive analysis of the bunches of grapes. Doing so will reduce the amount of pesticides on vines, while also protecting farmers from inhaling toxic chemicals.
Harvesting in agricultural robotics
As regards the use of robots in the agricultural harvesting phases, the work to be done is greater in spring and summer. Given the reduced workforce that makes it difficult to keep pace with the nature necessities, the products fall from the trees and often rot on the ground, releasing harmful greenhouse gases to the environment.
A number of robotic farmers who manage multiple crops simultaneously could be the best solution for agricultural harvesting. The robots would not replace humans, but would help workers to be more effective and constant, for example working all day and resisting extreme temperatures. All this enable to bring quality products to consumers’ tables, collected in the right period respecting the nature’s time.
You may also be interested in:
DRONES IN AGRICULTURE AND AGRITECH
PRECISION FARMING AND AGRITECH REVOLUTION